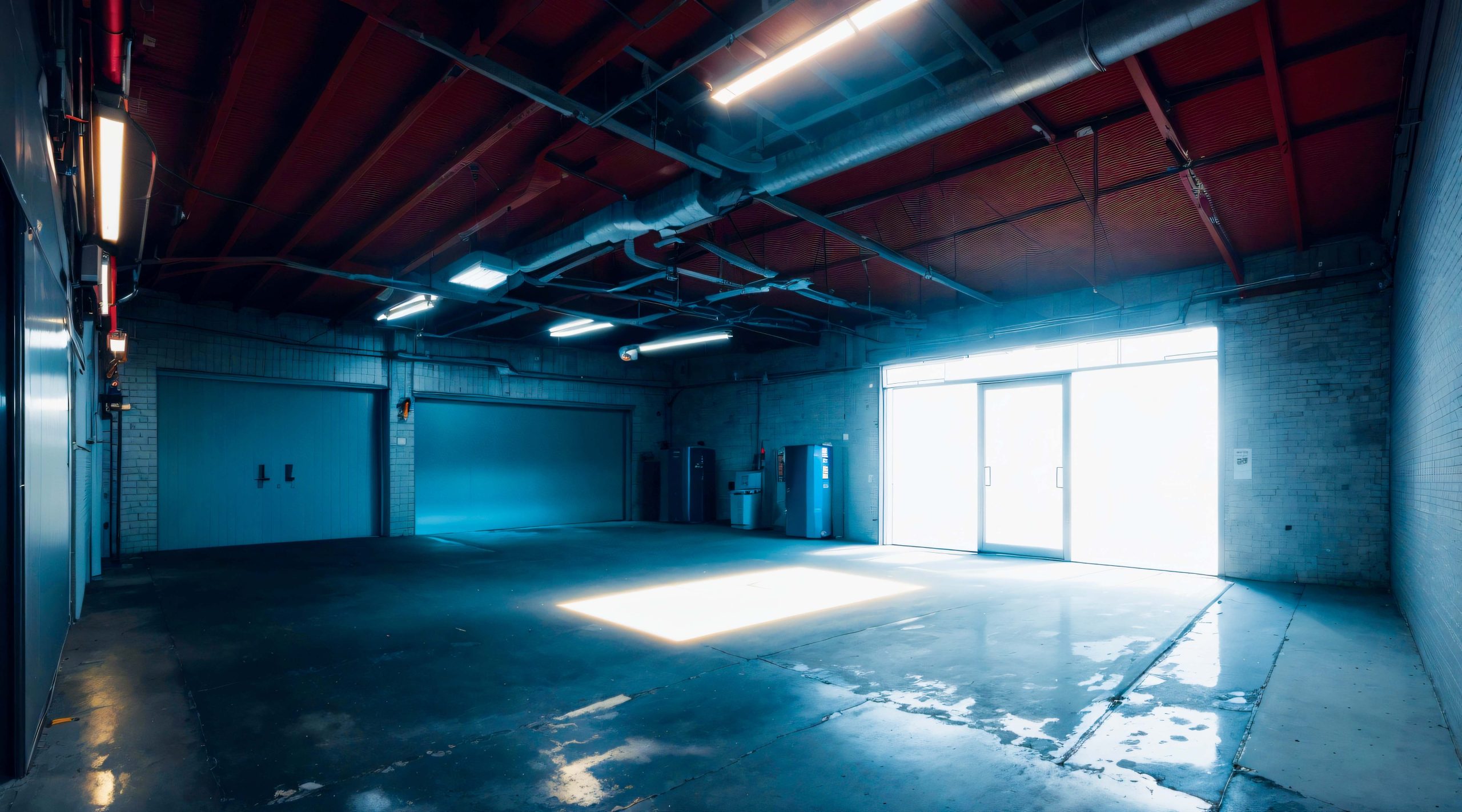
You have probably seen the viral TikTok clip where Elon Musk is asked about the biggest challenge facing humanity. His answer? “Population collapse.”
Now, the Tesla CEO is a known provocateur, and his sensationalist views have since been debunked by demographers. But there is a kernel of truth to his response.
According to Canadian scientist Vaclav Smil (who also happens to be one of Bill Gates’ favourite authors), birth rates in major western economies are teetering on the brink, either just below or above what he calls replacement levels — that is, the rate at which a country’s population has enough babies to sustain its own organic growth. In his book Numbers Don’t Lie, he defines the replacement birth rate at 1.7%. Guess where Canada stands? 1.4 per cent, as per Statistics Canada data from 2020.
Low birth rates, population collapse and demographic shifts may seem heavy-handed for a discussion on technician shortage. After all, hasn’t the industry been talking about the impending “mechanicalypse” since the turn of the millennium? The projected collapse surely hasn’t come to pass. But increasingly data seems to suggest that we may be closer to a crisis than we think.
A recent report from the Motor Vehicle Retailers of Ontario (MVRO) and the Canadian Automobile Dealers Association (CADA) shows that we are in uncharted waters now. According to the study, there were over 3,000 open jobs in automotive in Ontario in the first quarter of 2023 — double the number of what was seen before COVID.
Even more dire are the sustained trends. Between 2016 and 2021, the 55-plus group of technicians increased by about 13 percent, while 15-24- and 25-54-year cohorts dropped by 2 and 8 per cent, respectively. As the nation ages, these numbers will only accelerate.
One could argue that every industry faces a labour shortage post-COVID, and time may sort out the challenge. That may be true of industries such as software, but skilled trades — especially automotive — have a much wider, and deeper, problem.
Data from the U.S. further reinforces the crisis. The National Automobile Dealers Association (NADA) reported earlier this year that there are only 39,000 new technicians coming out of colleges every year compared to the approximately the 79,000 new jobs that are posted annually.
The problem is worse for diesel trucks. A recent Fleet Owner article shows there are 80,000 open jobs for every 10,000 diesel technicians added every year in the U.S. These shortages in the freight sector have ever bigger implications for our economy — impacting everything from flow of goods to inflation and everything in between.
One could argue that every industry faces a labour shortage post-COVID, and time may sort out the challenge. That may be true of industries such as software, but skilled trades — especially automotive — have a much wider, and deeper, problem. Part of the problem stems from systemic demographic shift and sustained decline in birth rates — countries such as Canada are just not being able to replenish its labour force. COVID may have fast-tracked the gap between retirees and new entrants, but that was coming one way or another.
But the bigger issue lies in the diminishing lure of vocational jobs. A survey conducted by 3M Canada found that 76 percent of young people do not want to pursue a career in a skilled trade. Other reports point to the same conclusion: Gen Z is simply not interested in being an automotive technician or a plumber.
We are largely to be blamed for the current situation. We, as a society, have long-favoured white-collar jobs over vocational ones — pushing kids to the more hallowed path of the four-year college degree. Many high schools do not even offer classes or certifications for skilled trades. Female students, who have made great inroads into white-collar professions, are rarely encouraged to become technicians.
Targeted immigration is a potential fix. Many Ontario dealers are actively working with their trade associations and government to bring in workers from overseas. Aftermarket shops could potentially benefit from these programs as well. Various provinces are also stepping up support for skilled trades — including automotive — in the form of both funding and training programs.
But these are mere band-aids. As older mechanics exit the workforce in larger numbers, it would be impossible to constantly replace them with foreign workers.
We are largely to be blamed for the current situation. We, as a society, have long-favoured white-collar jobs over vocational ones — pushing kids to the more hallowed path of the four-year college degree.
Rather, we need to change the conversation around technician jobs and foster recruitment from within. Tomorrow’s mechanics will require advanced technical knowledge to work in shops. We need to position these jobs as those of the shiny future, and not of the grimy past.
Students need to be made aware that modern automobiles are closer to computers than cars. Going forward, they would need functional knowledge of software, modern EV architecture, and artificial intelligence. Industry stakeholders — automakers, dealers, workshop chains — need to provide more “arsenal” in the form of simulators, advanced tools and marketing materials to vocational teachers and schools.
The demographic time bomb is ticking. Scientist Smil claims that once the birth rate falls below the replacement rate, it’s nearly impossible to turn it around. While broader policy will ultimately impact how we maintain the balance between retirees and young jobseekers, the auto repair industry will need to get creative in attracting talent. Can it make the mechanic “sexy” again? Maybe that’s another question for Elon Musk.
Related Posts
Comments
-
Neglecting the need for skilled tradesmen has been going on since the 70s
It’s long overdue for educators to change their approach to the trades
Some of it simply starts at home -
As someone who works as a technician, I have to say I cannot blame people for going into the white collar fields. Yes, right out of school I was making more money than my college educated counterparts, but as the years have gone on most if not all of them are making 50-100% more than me.
In addition to compensation there is a clear cultural difference. Office workers are treated as professionals (generally) and have comfortable working environments, work from home partially, and do not have to spend a dime of their own money (yes I am talking about the $100-$300 weekly tool payments I had for years) to complete the job.We can talk all day about vehicles being big computers and having all sorts of technology, but at the end of the day you have to be equally interested in getting dirty, hurt, bleeding, and working on things that were not designed to be easily serviceable and are incredibly frustrating.
Moving jobs consistently and working my way into management was the only way I was able to feel respected, treated as a professional, and not in pain at the end of a work week.
Not everyone is cut out to be a manager or sit at a desk all day, but there are certainly more lucrative trades that do not require as many different skill sets or capital to get started.
Not sure how to correct this issue, but that is my rant.
-
In 2021, I got into the automotive field with the desire of becoming a diag tech. I completed tech school, learned wiring diagrams, labscope, voltmeter, practiced on my own vehicles. A euro specialty shop hired me and honestly, I quickly began to regret my decision. The shop provided the tools and their master techs allowed me to grab whatever I needed from their huge tool collection. With each job, I began to realize that I was going to have to invest a ton of cash on tools. Sometimes, I struggled finding complete service info or wiring diagrams on certain vehicles. It was really frustrating. I ended up quitting on my 6th month and began working in a completely different field. Two years later, a new shop opened near my home. The owner had a good reputation. Well, I got a job there, in attempt to jump start my automotive career.. I ended up quitting on the 2nd week. That desire of wanting to become a diag tech (or a tech, in general) was long gone. It’s the working conditions, crappy pay, body aches, and huge tool investment that did it for me. These days, I’m no longer in automotive and looking at other career options. A lot of my former tech school classmates left the field after the first year.
-
Leave a Reply