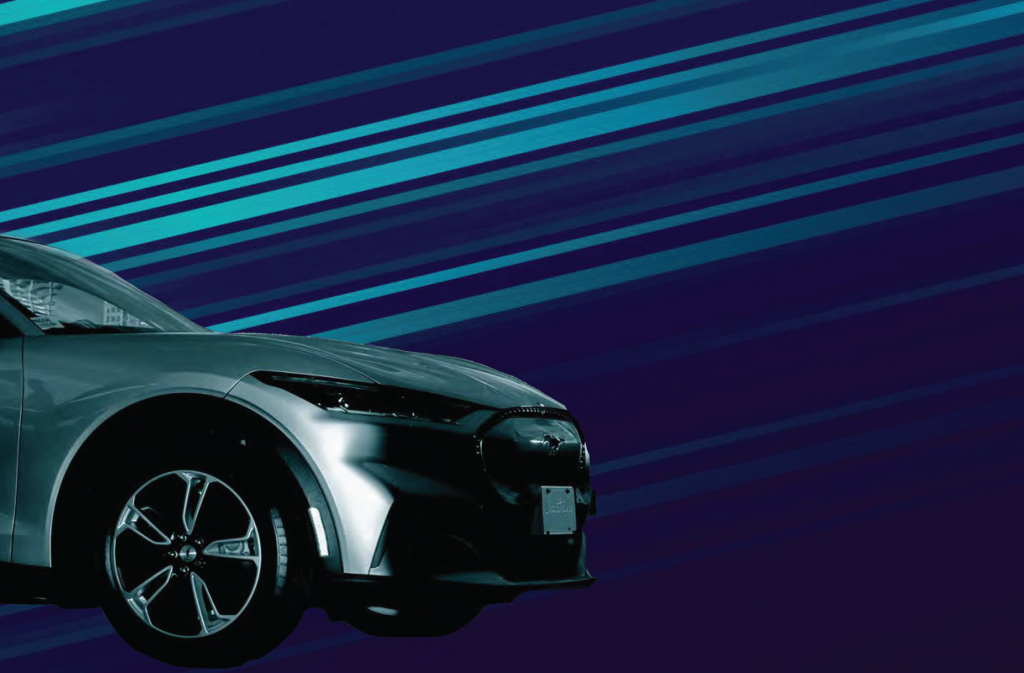
Electric vehicles will change how automotive repair shops service vehicles. But there will one at least area that may require more frequent service — and potentially greater repair opportunities.
As shops see more EVs in their bays, they will want to take a closer look at the vehicle’s ride control components, an area that experts are flagging as a concern in EVs that wouldn’t be as frequent in a traditional-powered vehicle.
In a report from the Auto Care Association and the Automotive Aftermarket Suppliers Association, several aftermarket opportunities with EVs were highlighted. Ride control was one as where parts can wear down quicker in an EV compared to an internal combustion engine vehicle.
Electric drive motors can provide high torque at starting speeds. This may affect the life of half shafts, CV joints, tires and other undercar components, said Carlos Thimann, director at Strategy&. Along with Akshay Singh, partner at Strategy&, he authored the report entitled Impact of New Technologies in the Automotive Aftermarket. It was presented at AAPEX 2021 in Las Vegas.
They wrote in the report that there have been multiple reports of high wear on electric vehicles.
“Even though a lot of this might be engineered into the product, it could be a situation where there might be some impact to the life of half shafts or CV joints,” Thimann said at AAPEX.
This indeed appears to be what’s happening, noted ride control experts.
“While many EVs currently utilize similar undercar platforms as their fossil-fueled counterparts, the increase in weight and torque of an electronic drivetrain can put more stress on undercar components,” said Andy Castleman, brand manager at Indiana-based KYB Americas Corporation.
One issue is a lower centre of gravity on electrics, observed Victor Moreira, technical services manager at Mevotech in Toronto. “All of these factors work together to add an increased amount of strain on undercar components, causing them to wear in a shorter amount of time when compared to a traditional vehicle.”
“The aftermarket must be able to supply the components and provide the knowledge to service providers on how to diagnose and maintain EVs.”
Original equipment manufacturers and, in turn, aftermarket companies, will need to figure out how to make stronger, lighter components to counter the added weight and drivetrain stress, Castleman said.
“Lighter components will also help to increase the range of the EV,” he added.
These are complicated and sophisticated systems, Castleman observed, and it’s up to the aftermarket to ensure the right guidance and education is given to support these products. He recommended distributors and wholesalers work with manufacturers that provide training and online support for these such technologies.
Furthermore, challenges are being presented by complex shapes and materials and design space constraints, Moreira told CARS.
“We also need to take the component’s strength-to-weight ratio into consideration when adapting the materials used. With EVs, even the magnetization of components during manufacturing may need to be addressed with a demagnetization process, in order to prevent any potential interference with the vehicle’s electronic systems,” he added. “Applying the correct detailed analysis and having a true understanding of these elaborate systems are really the only solutions to successfully working around these challenges.”
Shop concerns
For now, shops will use standard shocks, trusts and ride control components in general on EVs. However, major changes will be internal, noted Castleman. Manufacturers will adjust valve codes and spring rates to fit the increased torque and weight of the EVs.
“Technicians need to understand that, like gas vehicles, the EV undercar components will wear and need to be replaced,” he said. “Replacing ride control on [electric] vehicles will ensure the vehicles performed as they were originally designed.”
Furthermore, Castleman added, the lifespan of an EV will mean technicians will be replacing ride control and undercar components.
“Existing installation techniques will continue to be effective until, or if, new technologies and designs specific to EVs are developed,” he told CARS.
“Everything from the complex shapes and materials being used in control arms to the design space constraints of the vehicles can present potential challenges that need to be worked around.”
But changes have been taking place for many years now, Moreira said. He stressed the importance of technicians referencing the vehicle’s service manual to ensure all steps, from diagnostics to final installation, are done correctly. The old ways of working are no more.
“The ‘prybar inspections’ widely used on chassis components are not acceptable on many late-model vehicles and can provide false failures and potentially damage the components being tested,” he explained. “The changes in materials and designs also mean that strict adherence to torque specifications is required when tightening fasteners. Over or under torquing a fastener can come with some fairly dire consequences, and it’s never been more important to ensure the right amount of torque is being applied.”
Technicians also need to be far more careful when removing worn parts. Material and component designs could lead to inadvertent damage.
“Gone are the days of removal by hammer and installation by impact gun,” Moreira said.
Shops should also be working with their jobber to ensure they’re aware of the parts needed, especially if the shop is seeing more EVs roll in. Jobbers need to know if certain parts are wearing out quicker or need replacing more often
“You want your jobber to be prepared so you can get your parts as fast as possible,” Castleman noted. “Passing on information about what parts are wearing the quickest and being replaced most often will help your jobber carry the correct inventory.”
Shops should also be checking in with their jobber about added features in ride control products.
“Having a good understanding of component upgrades and how they benefit the vehicle will help shops explain to their customers what is being installed on their vehicle and validate that the choice they made was educated, rather than just based on price point or availability,” Moreira said.
To be ready for change, both Castleman and Moreira stressed the importance of training.
“Having the right tools and training is imperative when it comes to being prepared for this new wave of change. Adapting the skillset of technicians to safely and correctly both diagnose and repair EVs is going to determine how successful a shop can be in building its reputation as a trustworthy EV repair facility,” Moreira said.
“Technicians should have the knowledge and experience needed to analyze issues with EV undercar components,” Castleman said.
This feature originally appeared in the June issue of CARS magazine.
Leave a Reply