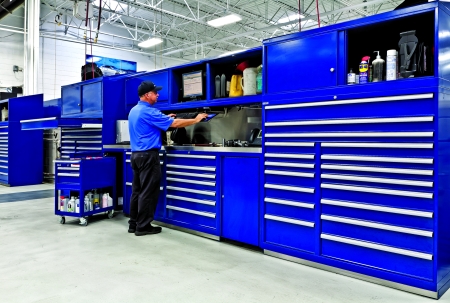
When a car dealership was looking to remodel its service facility, it wanted to do more than just shuffle tool boxes and parts storage around. In fact the new remodel removes traditional toolboxes altogether.
Tysinger Motor Company of Hampton, Virginia, recently completed a major facility remodel and wanted to provide a professional, organized and efficient layout in its Mercedes-Benz and Hyundai Service Departments.
Tysinger did an intensive search for a vendor eventually selecting Lista International, which had been involved in several of the dealership’s earlier successful remodeling efforts.
Working with Lista, Tysinger designed a system of integrated service bay technician toolboxes and workbenches that provide increased storage while promoting the professional image it was seeking. The new system even incorporates a full line of toolboxes for the night shift the dealership hopes to begin in the near future.
It wasn’t the first time the organization had sought to remodel its service facilities.
Tysinger was originally converted to the space savings and efficiency benefits of high density storage solutions more than two decades ago, when it was planning construction for a new dealership facility and found that construction costs were coming in way over budget.
At that time, using high density parts storage provided by Lista enabled Tysinger to lop off about 5,000 square feet in the parts department area, bringing construction costs down to an acceptable level. To make the new facility work, Lista spent more than a week inventorying the parts on hand so they could accurately lay out the new facility with cabinets of the proper height, drawer depth, and size.
While the original goal of installing high density storage was to be able to carry more parts in a smaller building footprint, an additional benefit turned out to be increased productivity with the same manpower, due to faster part retrieval time. According to Bob Rombs, Tysinger’s vice president, about 75-80% of all fast-moving parts can be stored at the parts counter.
“Retrieval time is cut in half because the cabinets, drawers and compartments are all labeled in a manner making it extremely fast and easy to find parts.” He adds, “This allows me to sell more parts with the same number of personnel.”
The Tysinger facility is virtually a block-square, 14-acre automotive campus, with separate Mercedes-Benz and Hyundai showrooms, and a combined service shop that is separated, but under one roof. Each brand has exclusive service reception, customer lounges, parts counters, cashiers and service lanes. As the dealership expanded over the years, additional high density storage solutions were incorporated to add to efficiency and provide space for parts and service. A 1998 project doubled the service and parts facility size, adding more Lista high density parts cabinets.
When Tysinger was looking to completely remodel their Mercedes-Benz and Hyundai service building with a professional appearance and a consistent look, they knew the key to success would be well planned and efficient technician work centres.
“If we had a clean sheet of paper, it would have been easier to develop a standard setup for every two service bays, but we didn’t have that luxury,” says Rombs, explaining that Tysinger was faced with a real challenge because it was remodeling an existing facility rather than building a new purpose-built one.
He cited just a few of the particular difficulties, including the presence of existing air lines, lifts (hydraulic, air and electric), and oil lines, as well as obstacles like water spigots and electrical connections already in place.
Realizing that high density storage was going to make or break the ambitious project, Tysinger looked at six vendors that it thought could supply the types of storage needed.
They ultimately selected Lista, based on the success of the earlier remodeling efforts, as well as the company’s attention to detail and quality products. Lista made multiple visits to look at the layout of the shop, and sat down with Rombs and the two service managers to determine what they would be looking for in technician work stations.
The information gathering phase included an entire day interviewing technicians, cataloguing every single one of the technician’s personal tool boxes, looking up the cubic inch storage capacity of all their toolboxes, and laying out a configuration for every single bay with the size of cabinets that would work in the space. Despite the existing features they had to work around, they were able to develop three standard configurations that could be used for the entire space. “To the outside observer it looks like they are all standard,” says Rombs.
The dealership knew that the key to making sure their technicians were satisfied with the new layout was providing ample storage space. They designed the work station setup to give every technician more cubic storage space than any had previously had with his own toolbox.
There was some initial concern among the technicians about having to give up their personal toolboxes. Making them an active part of discussions with Lista went a long way to meeting the twin goals of keeping the technicians happy and providing a professional appearance, with a uniform space that would be easy to clean and maintain.
The end product is a solution where one setup covers two service bays.
Each technician has his own section with a dealership-provided toolbox holding his own personal tools. In between is a shared work bench with a stainless steel top, overhead storage, and one PC work station in between. The PC is located in the middle;
Tysinger wanted to keep the workbench clear, so it designated a section in the center of the overhead storage to be used for the PC and monitor. The keyboard is on a special keyboard pullout tray provided by Lista, and phones are mounted on the workbench’s backsplash, leaving a clean workbench free of extraneous items.
Resistance to the project among the 34 technicians all but melted away after the installation, when technicians saw the high quality of the workstation and the amount of space they had to work with.
During the planning for the service area remodeling, Tysinger added one more goal into the mix.
They had long been toying with the idea of initiating a night shift without adding to the physical facility by increasing the number of service bays. The primary obstacle to adding the additional shift is where to store the toolbox, since they are so big and the facility had no space to stack the toolboxes during the day shift.
So, as they designed the new technician work stations, they added in extra space for a nightshift technician toolbox, built right into the unit, at the same height as a personal or roll around toolbox. They purchased additional toolboxes, each equipped with a separate key and lock and will be starting the night shift within the next year.
In a final nod to the consistent look they were seeking, Tysinger also purchased Lista cabinets for each of the four detailers in the Appearance Department, which are used to store polishing supplies, spray bottles, and polishing cloths.
Tysinger is extremely pleased with the results, chalking up the success to Lista’s efforts to really take the time to listen to their goals and objectives and understand what they were trying to achieve.
“They spec’d out products that will work best to meet our needs and continue to be extremely prompt about taking care of any problems or issues we encountered. I am impressed with the level of service and attention to detail for the layout they provided us.”
Leave a Reply