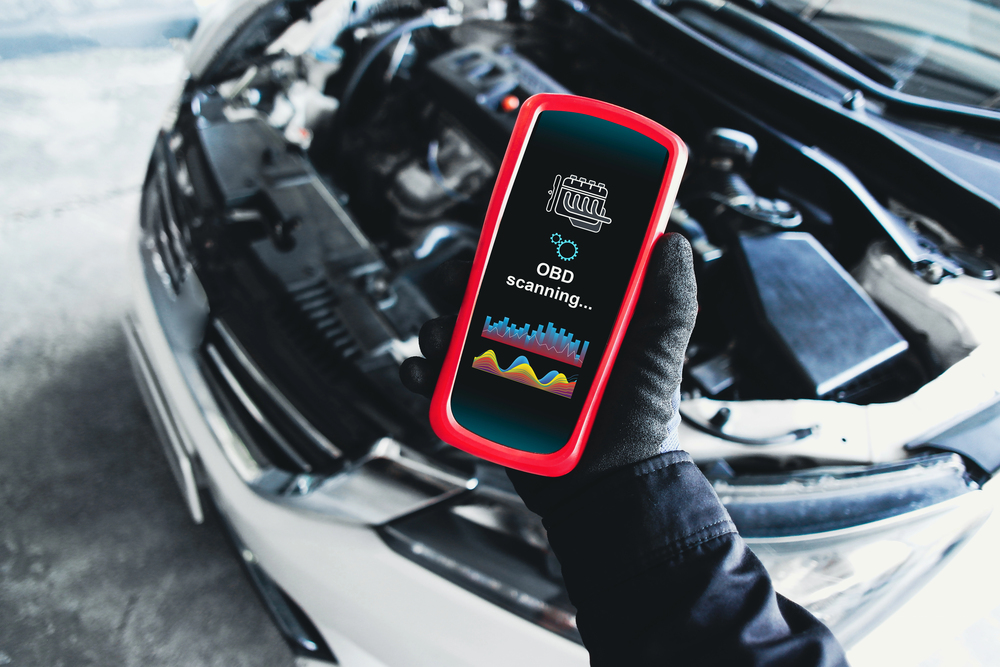
Selecting the right scan tool is crucial for automotive technicians, and understanding the options can help make the best choice for your shop. An expert recently laid out the decision-making process for picking the right one.
At the MEMA Aftermarket Suppliers Technology Conference, Donny Seyfer, executive director of the National Automotive Service Task Force, provided insights on how to choose the right scan tool for vehicle diagnostics.
Seyfer’s basic thought process begins with evaluating the volume of work on specific vehicle brands.
“If you’re working on a brand and it’s more than 20 per cent of your work, you’re going to be able to make the value proposition to own an OE tool for that,” he explained during the session, Bridging the Gap: Aftermarket Access to OEM Tools & Information for Vehicle Repair.
For specialists who primarily work on a single brand, using the same tools as the dealers makes sense. “Why not work from the same exact stuff the dealers are working from?” he added.
However, Seyfer acknowledged that there are other viable options. Aftermarket tools, while potentially lacking some features, are designed based on the needs of their primary customers.
“They, as a company, have to make a decision: ‘If I put every single feature on, is anybody going to use them? And who’s my customer? Who’s my customer that’s going to buy the most from me, and what do they need for features,’“ Seyfer noted.
This business case approach helps aftermarket tool manufacturers cater to the most relevant features for their users.
Another option is leveraging remote diagnostic services, which are offered by several companies designed to service the automotive aftermarket. This approach is beneficial for shops that do not frequently work on certain brands but still want to offer comprehensive services.
“I don’t work on Volvos very often, but I want to be able to offer a full service to my customers. So if they own a Volvo and a Subaru and a Ford, I want to be able to work on all of those cars,” Seyfer explained as the rationale for a shop owner to use these services.
By involving remote talent, shops can avoid the financial burden of investing in tools for infrequently serviced brands. “That investment’s only when you need it,” he emphasized.
Seyfer also highlighted the availability of OE tools on flexible subscription models. These short-, mid-, and long-term subscriptions allow shops to access the latest tools as needed without the ongoing cost of ownership.
“You can download the latest and greatest OE tool the day you need it and use it for 24 or 72 hours, or whatever their deal is,” he explained. “And then it’s not sitting there costing you money on the shelf.”
This flexibility enables shops to use aftermarket tools for general diagnostics and reserve OE tools for more complex systems, he added.
Image credit: Depositphotos.com
Leave a Reply